Владимир Одобряев,
Николай Татаринцев
Применение программируемых
контроллеров OMRON
в управлении непрерывными технологическими процессами
Программируемые логические контроллеры (PLC) корпорации OMRON (Япония) делятся на четыре класса: Micro (микро), Small (малые), Medium (средние) и Large (большие). Широкое применение в системах автоматического управления (САУ) непрерывными технологическими процессами получили PLC классов Medium и Large. Сбалансированная совокупность основных характеристик и функциональных возможностей PLC этих классов определило их преимущественное использование в САУ наиболее ответственными объектами. К их числу относятся бортовые установки космических агрегатов, системы управления процессами ядерных технологий, объекты военно-промышленного комплекса, объекты теплоэнергетики. Новой разработкой в этом классе изделий являются программируемые контроллеры серии SYSMAC CS1 (рис. 1).
Рис. 1.
Контроллеры серии CS1 по функциональным возможностям и техническим характеристикам существенно превосходят ранние модели PLC фирмы OMRON, а также изделия известных мировых фирм, находящихся в этом классе (класс — Medium). Ниже приводятся некоторые (общепринятые для программируемых логических контроллеров) параметры PLC CS1:
1. Быстродействие (время исполнения инструкции LD) — 0,04 мc.
2. Количество инструкций — более 400.
3. Количество точек ввода/вывода — 5120.
4. Емкость памяти программ — 250 Ksteps.
5. Емкость энергонезависимой памяти данных (DM)— 448 Kwords.
6. Емкость карты Flash-памяти — 48 МВ.
7. Номенклатура поддерживаемых модулей (ввода/вывода, специальных, коммуникационных) — более 100 типов.
8. Сети и интерфейсы:
— Ethernet (FTP, TCP/IP, UDP/IP);
— Controller Link;
— PC Link;
— DeviceNet (CompoBus/D);
— CompoBus/S;
— ProfiBus/DP;
— Host Link;
— NT Link;
— Protocol Macros;
— Peripheral Bus.
Рис. 2.
В настоящее время выпускается 9 моделей модулей центрального процессора контроллеров серии CS1. Между собой модули CPU (рис. 2) отличаются количеством бит I/O (минимально 960 бит I/O для CS1G-CPU42; максимально 5120 бит I/O для CS1H-CPU67), емкостью программ (минимально 10 Ksteps для CS1G-CPU42; максимально 250 Ksteps для CS1H-CPU67), размером памяти данных (минимально 32К слов для CS1G-CPU42; максимально 448К слов для CS1H-CPU67), наличием или отсутствием EM-памяти. Широкая сетка (рис. 3) взаимных сочетаний названных параметров позволяет произвести оптимальный выбор модуля CPU для конкретного технологического процесса. Все типы модулей CPU снабжены коннектором для установки карты Flash-памяти, периферийным портом и портом RS232C, а также имеют отсек для установки дополнительных коммуникационных плат.
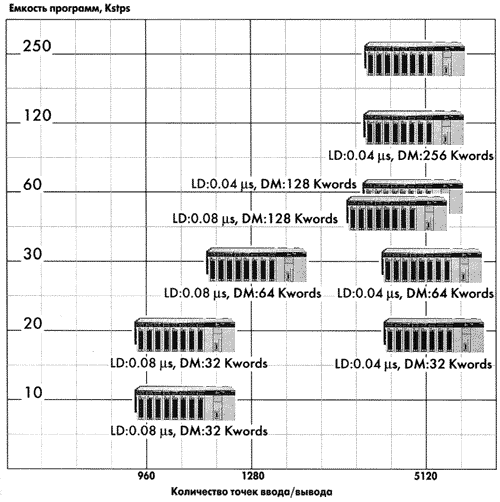
Рис. 3.
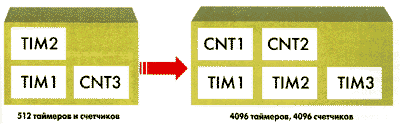
Рис. 4.
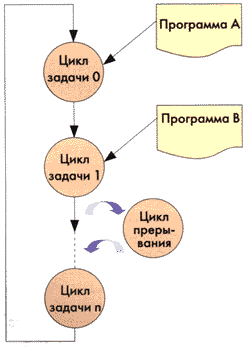
Рис. 5.
Качественно изменились некоторые ранее существующие инструкции процессора и добавились новые, упрощающие программирование сложных алгоритмов. В частности, такие инструкции, как таймеры и счетчики, ранее принадлежали одной области памяти (не могли иметь одинаковые номера в одной программе), и их общее количество для контроллеров, как правило, не превышало 512. В программах контроллеров CS1 можно одновременно использовать таймеры и счетчики с одинаковыми номерами (рис. 4). Тех и других может быть по 4096. Появились новые инструкции, позволяющие обрабатывать файловую память, текстовые строки, индексные регистры и многие другие. Используя их, модуль CPU может манипулировать своей собственной памятью. Так, например, из программы лестничных диаграмм можно осуществлять весь набор операций над файлами, расположенными на карте памяти (удалять, копировать, создавать директорию и изменять ее имя). Программу пользователя, находящуюся в CPU модуле, можно заменить программой из карты памяти, не выключая контроллер, и без применения средств программирования. Программу пользователя и областей данных можно автоматически сохранить на карте памяти при включении питания («легкое сохранение»). В случае обнаружения неисправности все данные, расположенные в модуле CPU, будут сохранены мгновенно. Это особенно важно для систем управления с повышенными требованиями к надежности.
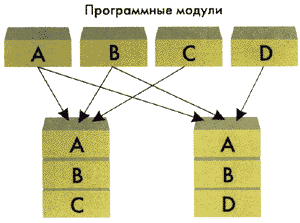
Рис. 6.
В качестве базовой концепции предложено структурное многозадачное программирование (Task Programming). Программа в PLC серии CS1 разделена на задачи (циклические задачи), которые выполняются в установленном порядке (рис. 5). Программы прерывания тоже введены как задачи (задачи прерывания). Контроллеры CS1-серии поддерживают до 32 циклических задач, 32 задачи прерывания I/O, 2 задачи запланированных прерываний, 1 задачу прерывания при отключении питания и 256 задач внешних прерываний. Программы задач создаются в виде модулей с отдельными функциями и целью. В дальнейшем эти модули могут использоваться при написании программ для аналогичных по функциональному назначению систем (Рис.6.).
Введение структурного программирования преследует следующие цели:
- стандартизация программ, как модулей;
- разработка программ несколькими программистами, работающими параллельно;
- создание программы, более легкой для понимания;
- создание программ по шагам;
- использование BASIC-подобных мнемонических инструкций для написания программы, что трудно сделать при лестничном программировании (таких как условные переходы и циклы).
Появление новых инструкций позволяет упростить и саму процедуру программирования. В частности имеется возможность:
- создавать циклически повторяющиеся программные секции;
- осуществлять косвенную адресацию слов;
- использовать индексные регистры как указатели косвенных адресов в адресном пространстве данных (Индексные регистры очень удобны в комбинации с циклами, инкрементными инструкциями и инструкциями обработки табличных данных, поддерживаются авто-инкремент, авто-декремент, а также функции ветвления.) и т. п.
Несмотря на наличие мощных функциональных возможностей PLC, задача разработки и программирования ряда систем с непрерывными процессами по-прежнему остается весьма сложной. Особенно это касается систем управления объектами с взаимосвязанными контурами регулирования (например, объекты теплоэнергетики, нефтяная, химическая, газовая промышленность, металлургия). Для облегчения и эффективного решения этих задач фирмой OMRON разработан специальный модуль управления контурами регулирования LCU (Loop Control Unit) и соответствующее к нему программное обеспечение CX-Process Tool и CX-Process Monitor. Программный пакет CX-Process Tool служит для комбинирования функциональных блоков и установления программных связей между ними, а CX-Process Monitor — для мониторинга системы. Указанные средства позволяют достаточно легко «пройти» путь от функциональной схемы до мониторинга спроектированной системы. На рис. 7 показана простейшая схема каскадного управления и структура используемых ее блоков. Для ее реализации потребуются модули ввода/вывода аналоговых сигналов (2 ввода, 1 вывод) и модуль LCU.
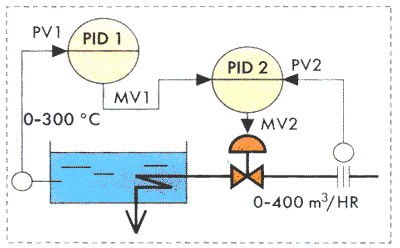
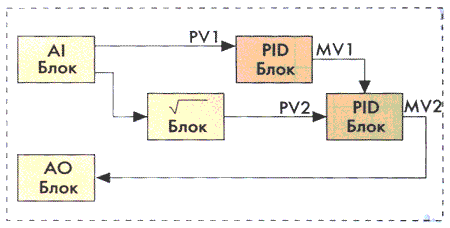
Рис. 7.
Связь аналоговыми сигналами между блоками определяется программно, в среде CX-Process Tool (рис. 8).
Для мониторинга системы управления достаточно по последовательному каналу соединить PLC с компьютером, на котором установлен программный пакет CX-Process Monitor (рис. 9).
Научно-производственная фирма «РАКУРС» (Санкт-Петербург) имеет богатый опыт в разработке систем управления на базе программируемых контроллеров фирмы OMRON. За последние пять лет было разработано и сдано «под ключ» более 50 крупнейших объектов на территории России и за ее пределами. На объектах теплоэнергетики широко используется программно-технический комплекс (ПТК) «ОМ-мега», разработанный ООО «НПФ «РАКУРС» в соответствии с ТУ 4252-001-27462912-98 и являющийся средством измерения, имеющий сертификат «утверждения типа средств измерения» RU.C.34.022.A № 6090 и сертификат соответствия РОСС.RU. АЯ43.В02146 № 3114659.
Рис. 8.
ПТК построен на базе контроллера управления технологическим процессом, представляющего собой программируемый логический контроллер со специальным модулем управления контурами регулирования (LCU) и необходимым набором модулей аналогового и дискретного ввода/вывода (I/O).
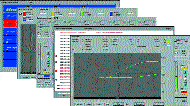
Рис. 9.
Основные преимущества систем управления, выполненных на базе PLC+LCU:
- Стоимость значительно ниже по сравнению с традиционными системами DCS;
- Занимает в 4-5 раз меньше места;
- Не требует создания специальных климатических условий, может быть установлен непосредственно в машинном зале.
Имея аналогичные средства для разработки программного обеспечения и выполняя те же функции, система управления непрерывными технологическими процессами на базе PLC+LCU становится достойной альтернативой традиционным системам DCS.
info@rakurs.spb.ru
|