Выбор метода депанелинга
Все возрастающий спрос на максимальную функциональность электронных устройств,
качество и безотказность работы при одновременном уменьшении габаритов и цены, конкуренция на рынке ведут к повсеместному внедрению автоматизированных процессов производства и стремительному уменьшению доли ручного труда.
Разработчики оснастки производства существенно расширяют технологические возможности производственников, предлагая широкий спектр автоматического оборудования для процессов заключительной части цикла производства электроники: установка крупногабаритных компонентов на ПП, пайка, разрезка ПП (депанелинг), сборка ПП в корпус электронного устройства, тестирование, маркировка, упаковка и т. д. Автоматизация этих процессов существенно улучшает качество выпускаемой продукции, увеличивает объемы производства, снижает себестоимость продукции, дает неоценимую поддержку процессам управления производством и в конечном итоге ведет к ощутимому повышению конкурентоспособности предприятия в целом.
Технологии депанелинга
Депанелинг — это удаление обрезков и прочих отходов, возникающих при вырезке одинарной печатной платы (ПП) или разделении нескольких ПП, заключенных в одну большую панель (рис. 1).
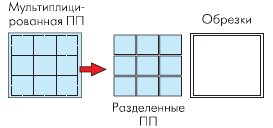 Рис. 1
В технологической цепочке операция депанелинга стоит после фазы установки компонентов на ПП. Поэтому стоимость промежуточного продукта, поступающего после операции сборки на фазу депанелинга, а следовательно, и стоимость производственного брака на этом этапе, весьма и весьма высока. Таким образом, несложное, казалось бы, определение сути процесса отражает его решающее значение во всем цикле производства ПП.
Эта простая технологическая операция может принести много хлопот производителям ПП, поэтому производителями технологического оборудования предлагается широкий спектр решений по автоматизации процесса, включающий порой весьма сложные и дорогие решения этой «простой» проблемы. Для своих систем депанелинга фирма JOT Estonia выбрала фрезерование в качестве основной технологии. На наш взгляд, эта технология наиболее удачна на данный момент. Ниже приводится обзор альтернативных методов депанелинга, предлагаемых производителями технологической оснастки.
Ручной депанелинг
Единственное преимущество данной технологии по сравнению с другими — невероятная гибкость процесса. Не требуется никакой смены оснастки и перепрограммирования. Все, что нужно здесь — умелые руки работника. Это соображение до сих пор привлекает некоторых производственников. Для подавляющего же большинства данная технология абсолютно неприемлема. Критические недостатки метода очевидны: прилагаемые нагрузки разрушают компоненты, смонтированные на ПП, и паяные соединения, а порой вызывают расслоение ПП. Вся работа, проделанная на предыдущих технологических этапах, часто идет прямиком в мусорную корзину.
Желательно также, чтобы выламываемая ПП имела прямые линии разлома, а это довольно редкое явление для сегодняшних продуктов. Подготовка линий для разлома достигается путем предварительного скрайбирования или сверления ПП в местах разлома. Сам процесс неточен и требует большой доли ручного труда, что ведет к увеличению времени цикла производства продукта и затрат в целом, большому количеству технологического брака.
В качестве примера рассмотрим производство мобильных телефонов. Типичное время такта всего завода — готовый телефон за 15 с максимально при работе в 3 смены по 50 недель в году, что дает около 1 730 000 телефонов в год. Себестоимость одной ПП для мобильного телефона составляет в среднем примерно 75 EUR, розничная цена телефона в среднем 280 EUR. Уровень брака при ручном депанелинге в самом оптимистичном случае 0,5%. Таким образом, производственные потери составят 648 750 EUR и потери от несостоявшихся продаж по вине производства составят 2 422 000 EUR. Общий убыток –3 070 750 EUR.
Резка на гильотине
Данный метод позволяет резать сплошные линии либо срезать отдельные перемычки ПП. Можно резать вручную либо на автоматическом прессе. Метод довольно производителен, но прилагаемые напряжения велики и здесь. К тому же длина реза часто ограничивается длиной лезвия. Этот метод больше подходит для мелких серий и экспериментальных образцов. В этом случае могут быть повреждены компоненты, установленные на поверхность ПП.
Депанелинг с предварительным скрайбированием заготовок ПП
Процесс скрайбирования представляет собой фрезерование V-образных канавок (линии будущего разлома) на обеих сторонах ПП при помощи дисковых фрез для последующего разделения ПП. Это довольно быстрый и надежный метод подготовки ПП, но применим только в случае прямых линий контура ПП.
Разделение ПП после установки электронных компонентов в этом случае происходит вручную или с помощью специальных устройств. Устройства снабжены лезвиями, которые делаются в виде пары дисков либо в виде диска и прямого лезвия. ПП подается между дисками. Диски пробегают по предварительно нанесенным на обе поверхности V-образным канавкам, определяющим линию реза. Благодаря геометрии профиля канавки диски создают существенные латеральные разрывающие усилия. Диски, таким образом, не режут, а больше расталкивают части ПП друг от друга в противоположные от канавки стороны.
К недостаткам метода относятся порой значительные усилия, прилагаемые к ПП во время обработки, что ведет к повреждению паяных соединений, расположенных вблизи места реза и к расслоению материала ПП, а в случае с ручным разделением — к повреждению компонентов от прилагаемых рукой усилий; кроме того, здесь необходим оператор. Свобода конструирования ПП, а следовательно, и устройств, в которые она входит, ограничена применением только прямых сквозных линий контура ПП.
Штамповка
Технология предусматривает применение пресса для выдавливания ПП из панели. Метод обладает одним существенным преимуществом: очень быстрый процесс; в случае многомодульной ПП все модули выдавливаются одновременно. Также форма ПП может быть произвольной, но линия среза не может быть сплошной — рекомендуется ПП с отдельными удаляемыми мостиками, нежели удаление материала со всей линии среза. Вследствие значительных усилий при штамповке объем производственного брака также остается высоким. Предлагаемые на рынке решения часто требуют ручной загрузки и выгрузки продукции из штампа, поэтому данный процесс сложно встроить в автоматическую производственную линию. Дорогая оснастка: цена штампа может достигать 5000 EUR и для беспрерывного производства необходимо иметь как минимум один штамп в запасе для предотвращения простоев вследствие поломки штампа.
Среднесерийное производство 10 разных продуктов требует оснастки в 20 штампов, что дает инвестицию в 100 000 EUR. Этот метод может быть разумным выбором для крупносерийного производства, ориентированного на узкую номенклатуру выпускаемой продукции.
Резка дисковой пилой
Преимущества:
- высокоскоростной процесс — скорости резания в 3–5 раз выше, чем для роутинга;
- минимальные усилия на ПП;
- хорошее качество кромок;
- минимальная толщина режущего диска.
К недостаткам относится возможность резания только прямых линий. Технология хорошо применима при вырезке большого количества модулей из одной большой ПП.
Резка лазером
Это довольно новая технология находится в фазе своего становления, хотя некоторые фирмы уже предлагают готовые разработки. Преимуществ очень много: отсутствие пыли, возможность обработки широкой номенклатуры перспективных и классических материалов ПП, скорость, точность.
Недостатков тоже хватает: все еще очень высокая стоимость оборудования, большие расходы на содержание, высокие требования к обслуживающему персоналу, жесткие требования к безопасности. Для ПП это интенсивный нагрев прилегающих к зоне резания областей, вероятность образования нагара на кромках, отсутствие надежных решений для обработки многослойных ПП.
Фрезерование концевой фрезой (routing)
Технология подразумевает удаление соединительных мостиков или выпиливание полного контура ПП. Для этого применяются различные типы фрез. Мостики перемалываются фрезой в пыль, и пыль удаляется интегрированным пылесосом. Технология обладает рядом существенных преимуществ: высокая скорость обработки, высокая точность, минимальные усилия, действующие на ПП, возможность обработки любых нелинейных контуров ПП, отличное качество обработанных кромок делают данную технологию наиболее предпочтительной из всех альтернатив. Технология позволяет производить быструю переналадку оборудования под разнообразную номенклатуру ПП. Данный метод применим для полностью автоматических систем, встраиваемых в линию, или автономных технологических систем.
Недостатком технологии можно назвать значительный уровень начальных инвестиций при покупке базового оборудования. Необходима эффективная система удаления пыли. Некоторые ПП сложной конструкции могут потребовать специализированных систем крепления.
Эти недостатки быстро окупаются вследствие значительного улучшения качества, высокой скорости обработки и уменьшения или полного исключения доли ручного труда, а также полного устранения брака, связанного с депанелингом, присутствующим в ручных методах.
Несмотря на возможность обработки очень широкой гаммы продуктов, данная технология все же накладывает некоторые ограничения на конструкцию ПП. Ширина реза менее 1,0 мм в рамках данной технологии подходит плохо и требует специализированных решений. Рекомендуемый диапазон — 1,5…3,0 мм. Для полностью автоматических систем, встраиваемых в линию, ПП до разрезки должна иметь с двух сторон участки шириной 2,5 мм минимум, необходимые для доставки ПП при помощи конвейера в рабочую зону (рис. 2). Если этой свободной полоски нет, то альтернативой будет применение автономной системы с ручной загрузкой ПП.
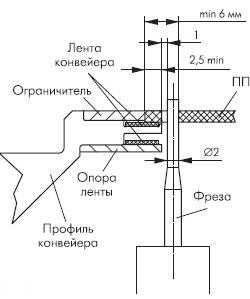 Рис. 2
Для фиксации мультиплицированной платы в процессе разделения в компании JOT Estonia применяются специальные фиксаторы, установленные по краям рабочей зоны на конвейере, а также модульные захваты, пальцы которого поддерживают и фиксируют каждый отдельный модуль (рис. 3). Количество модулей на захватах варьируется в зависимости от количества модулей на мультиплицированной плате, а в случае изменения обрабатываемых изделий смена захвата благодаря использованию стандартизированной головки на манипуляторе происходит в течение нескольких секунд. Возможные конфигурации захватов зависят от обрабатываемого продукта (рис. 4). Для автоматических систем, встраиваемых в линию, ПП должна быть достаточно жесткой и не допускать чрезмерного ее провисания на транспортирующем конвейере. Допустимое провисание — максимум 2,0 мм. Если жесткость
ПП недостаточна, то автономная система является хорошим решением.
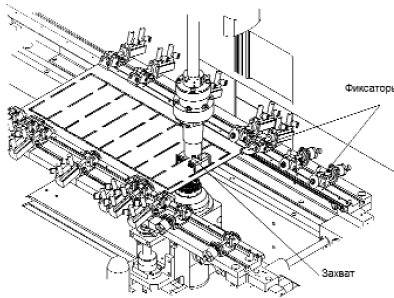 Рис. 3
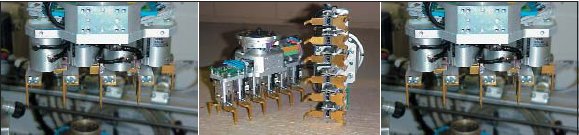 Рис. 4
Стандартная конфигурация встроенных в линию роботов JOT Estonia для депанелинга позволяет обрабатывать платы размером до 320x400 мм с точностью повторения позиций до ±0,02 мм.
Автономные системы представляют собой отдельно стоящие роботы (рис. 5), где загрузка-выгрузка продукта осуществляется не с помощью конвейера, а вручную (рис. 6).
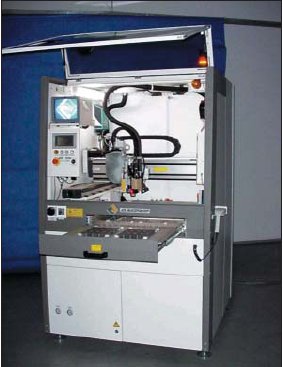 Рис. 5
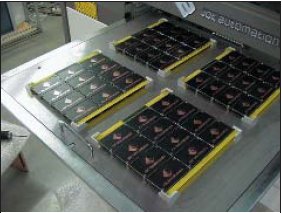 Рис. 6
В целях фиксации панели для фрезерования применяется система штифтов и прижимных масок с прорезями для движения фрезы (рис. 7). Но и эти системы позволяют получать криволинейный контур ПП, так как снабжены аналогичными манипуляторами, работающими в прямоугольной системе координат. Модели этой системы подходят для среднесерийных объемов производства с разнообразным ассортиментом продукции и позволяют обрабатывать мультиплицированные ПП размером до 520x520 мм, толщиной от 0,6 до 3,2 мм, с высотой установленных компонентов на нижней стороне ПП до 70 мм и на верхней стороне — до 30 мм.
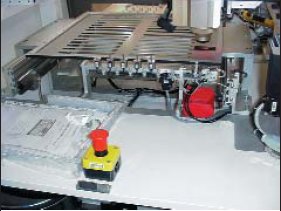 Рис. 7
Скорость процесса или время цикла как в автоматическом варианте, так и в варианте ручной загрузки-выгрузки продукта зависят от таких параметров, как толщина и слойность ПП, длина перемычки (мостика) или размера вырезаемого модуля. Неоспоримым преимуществом перед вышеописанными методами депанелинга является изначально заложенная в роботы компании JOT Estonia техническая возможность обрабатывать контуры любой конфигурации, что снимает ограничения по форме и позволяет придать конечному изделию новые потребительские качества. Это в конечном итоге способствует увеличению спроса на продукцию и росту доходов предприятия.
Проблема выбора
Часто основным критерием при определении необходимого уровня автоматизации является объем выпуска продукции и уровень необходимых инвестиций в автоматизацию. Разумный подход, но это далеко не все. Необходимо также учитывать форму и размер самой ПП, уровень ее технологической сложности, монтируемые компоненты и методы крепления на ПП, стоимость ПП.
Использование полностью автоматических систем в условиях массового выпуска одного типа несложной или недорогой продукции вряд ли оправдано, и упрощенный метод депанелинга (к примеру, штамповка) успешно решает поставленную задачу. И наоборот, при выпуске широкой номенклатуры сложных и дорогостоящих продуктов автоматическая система может окупиться в короткий срок благодаря низким потерям от брака.
Сама форма ПП может повлиять на принимаемое решение: удаление уже 15 перемычек на плате сложного нелинейного контура вручную — нелегкий труд.
Для правильного выбора нужно точно знать планируемые объемы производства, понимание сути процесса и знание предлагаемых на рынке оборудования возможностей. Решение об инвестициях в автоматизированные системы депанелинга возможны при тщательном анализе всех решающих факторов, включающих стоимость оборудования, экономию, полученную от улучшения качества, ускорение процессов обработки, снижение затрат, связанных с ручным трудом, тип продукции и номенклатуру. Улучшение качества всего на долю процента способно в итоге принести очень существенную прибыль, с избытком покрывающую инвестиции.
Михаил Кольцов
|